There’s a significant shift happening in the industrial landscape with the integration of Artificial Intelligence (AI) and Internet of Things (IoT) in what experts are now calling Industry 0. These cutting-edge technologies are revolutionizing traditional manufacturing processes by enhancing automation, predictive maintenance, and real-time data analytics. However, with great power comes great responsibility, as the need for robust cybersecurity measures to protect sensitive data from potential breaches is more crucial than ever. Let’s probe into the transformative impact of AI and IoT in shaping the future of Industry 0.
Key Takeaways:
- AI and IoT Integration: The integration of Artificial Intelligence (AI) and Internet of Things (IoT) technologies is revolutionizing Industry 0 by enabling machines to communicate, learn, and make autonomous decisions.
- Smart Manufacturing: AI and IoT are transforming traditional manufacturing processes into smart, interconnected systems that optimize efficiency, enhance quality control, and reduce downtime.
- Predictive Maintenance: AI algorithms analyzing IoT sensor data can predict equipment failures before they occur, allowing for proactive maintenance and minimizing production disruptions.
- Data Analytics: The combination of AI and IoT generates vast amounts of data that can be analyzed to uncover valuable insights, improve operational workflows, and drive strategic decision-making.
- Cybersecurity Challenges: As Industry 0 becomes increasingly connected and data-driven, addressing cybersecurity risks associated with AI and IoT technologies is paramount to safeguarding critical infrastructure and sensitive information.
The Evolution of Industry
From Industry 1.0 to Industry 4.0
For centuries, industries have undergone transformative changes, evolving from the manual labor-intensive processes of Industry 1.0 to the highly interconnected and technology-driven systems of Industry 4.0. Industry 1.0, characterized by the use of steam engines and water power, marked the beginning of industrialization. I
ndustry 2.0 saw the introduction of electricity, assembly lines, and mass production, revolutionizing manufacturing processes.
Industry 3.0 brought about automation through the use of computers and robotics, further increasing efficiency and productivity.
The Rise of Automation and Data Exchange
Exchange The advent of Industry 4.0 has ushered in the era of automation and data exchange, where machines are equipped with AI algorithms that enable them to communicate with each other and make decisions autonomously. This interconnected network of machines, known as the Internet of Things (IoT), has revolutionized the way industries operate, allowing for real-time data analysis, predictive maintenance, and improved decision-making processes.
From the automotive industry to healthcare and agriculture, the integration of AI and IoT technologies has paved the way for increased efficiency, reduced costs, and enhanced productivity. However, with this increased connectivity comes the potential vulnerabilities to cyber-attacks and data breaches, highlighting the importance of robust cybersecurity measures to safeguard sensitive information.
The Role of Artificial Intelligence
It is undeniable that Artificial Intelligence (AI) is revolutionizing multiple industries, including manufacturing. Through its ability to analyze data, identify patterns, and make decisions, AI is transforming traditional processes into smarter, more efficient ones. In the context of Industry 0, AI plays a crucial role in optimizing operations, enhancing productivity, and reducing costs.
Machine Learning and Predictive Maintenance
Any manufacturing plant knows the importance of keeping equipment running smoothly to avoid costly downtimes. This is where Machine Learning algorithms and Predictive Maintenance come into play. By analyzing historical data, AI can predict when a machine is likely to fail and schedule maintenance proactively. This not only prevents unexpected breakdowns but also reduces maintenance costs and extends the lifespan of equipment.
AI-powered Quality Control and Inspection
One of the key aspects of manufacturing is ensuring product quality. AI-powered Quality Control and Inspection systems utilize computer vision and deep learning algorithms to identify defects in real-time. These systems can detect even the smallest deviations from the set standards, ensuring that only high-quality products reach the market.
Learning from vast amounts of data, AI can continuously improve its accuracy in detecting defects, making the quality control process more efficient and reliable.
Intelligent Supply Chain Management
Maintenance, With the increasing complexity of global supply chains, managing inventory, logistics, and production processes has become a daunting task. Intelligent Supply Chain Management powered by AI can optimize these processes by analyzing data in real-time, identifying bottlenecks, and providing recommendations for improvement. By implementing AI-driven solutions, manufacturers can achieve greater efficiency, cost savings, and agility in their supply chain operations.
The Impact of Internet of Things
Keep in mind that the Internet of Things (IoT) has revolutionized the way industries operate by connecting devices and enabling real-time data monitoring and analysis. Through the integration of AI and IoT technologies, organizations can harness the power of interconnected devices to gather valuable insights and make informed decisions in Industry 0.
IoT-enabled Real-time Monitoring and Tracking
Monitoring: IoT-enabled real-time monitoring and tracking systems allow organizations to collect data from various sensors and devices in real-time. By monitoring key parameters such as temperature, pressure, and location, businesses can optimize their operations, improve productivity, and enhance safety measures.
Increased Efficiency through Sensor-based Automation
Through: Sensor-based automation, made possible by the IoT, is transforming industries by streamlining processes and increasing efficiency. Sensors embedded in equipment can detect issues, trigger automated responses, and even adjust settings without human intervention, leading to improved performance and cost savings.
Plus: With sensor-based automation, organizations can reduce downtime, minimize errors, and enhance overall productivity.
IoT-driven Condition-based Maintenance
One: IoT-driven condition-based maintenance utilizes real-time data from sensors to predict equipment failures before they occur. By analyzing the performance metrics of machinery, organizations can schedule maintenance proactively, avoid unexpected breakdowns, and extend the lifespan of their assets.
IoTdriven: Condition-based maintenance not only reduces maintenance costs but also enables organizations to optimize their resources and enhance operational efficiency.
Integration of AI and IoT
After establishing the importance of both Artificial Intelligence (AI) and Internet of Things (IoT) in Industry 4.0, it becomes crucial to explore how these technologies can be seamlessly integrated to maximize their potential and drive innovation in Industry 0.
AI-powered IoT Analytics for Insights
On the one hand, AI-powered IoT analytics play a pivotal role in extracting valuable insights from the vast amounts of data generated by interconnected devices. By utilizing advanced machine learning algorithms, organizations can gain actionable intelligence to enhance operational efficiency, predict maintenance issues, and improve overall decision-making processes.
IoT-generated Data for AI Model Training
Any successful implementation of AI in an industrial setting heavily relies on high-quality data for training machine learning models. In this context, IoT-generated data serves as a valuable resource for refining AI algorithms and improving predictive capabilities.
For instance, IoT sensors deployed in manufacturing plants can continuously collect real-time data on machine performance, energy consumption, and production output. This data, when fed into AI algorithms, can help businesses identify patterns, detect anomalies, and optimize processes to drive efficiency and productivity.
Seamless Communication between AI and IoT Systems
Insights on the Role of AI and IoT in Industry 0 would be incomplete without addressing the necessity of establishing seamless communication channels between AI and IoT systems. Ensuring interoperability and data exchange between these technologies is important for harnessing their combined power effectively.
To maximize the benefits of Industry 0, organizations must invest in developing robust integration frameworks that enable bidirectional data flow and real-time synchronization between AI algorithms and IoT devices, enabling quick responses to changing conditions and facilitating autonomous decision-making processes.
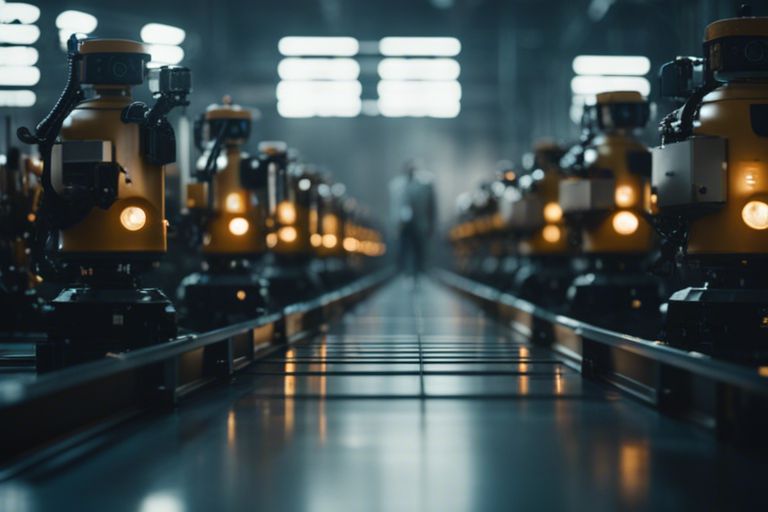
Applications in Industry 0
Smart Manufacturing and Production
All industries are gearing towards implementing smart manufacturing and production processes in Industry 0. This involves the use of AI and IoT technologies to create interconnected systems that can optimize operations, improve efficiency, and reduce downtime. By utilizing real-time data and predictive analytics, manufacturers can make informed decisions to streamline their production processes and keep up with the demands of the market.
Intelligent Logistics and Supply Chain Management
These technologies enable real-time tracking of goods, predictive analysis of consumer demand, and automated inventory management. This results in efficient supply chains, reduced costs, and improved customer satisfaction.
Supply chains in Industry 0 are becoming increasingly complex with global operations and the need for real-time responsiveness.
AI-powered Predictive Maintenance in Industry 0
All Logistics companies are embracing AI-powered predictive maintenance solutions in Industry 0 to prevent equipment failures and minimize downtime. By deploying sensors and AI algorithms, organizations can monitor the health of machinery and predict maintenance needs before issues arise. This proactive approach helps in maximizing operational efficiency and extending the lifespan of assets.
Intelligent use of AI and IoT technologies in Industry 0 is revolutionizing how companies manage their operations.
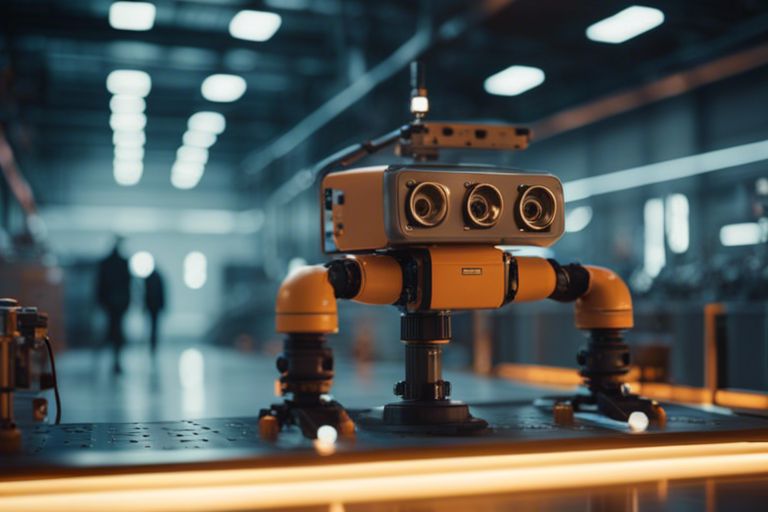
Challenges and Limitations
Data Security and Privacy Concerns
Privacy: Not surprisingly, one of the major challenges in implementing AI and IoT in Industry 0 is the concern over data security and privacy.
With a vast amount of sensitive information being collected and processed by interconnected devices, there is a heightened risk of unauthorized access and potential breaches.
Integration and Interoperability Issues
For: Another significant challenge revolves around integration and interoperability issues.
As different systems and devices need to communicate and work together seamlessly, compatibility issues can arise, leading to obstacles in the smooth operation of Industry 0 processes.
Furthermore, the integration of various technologies, protocols, and standards from different vendors can be complex and time-consuming. This can hinder the overall efficiency and effectiveness of implementing AI and IoT solutions in industrial settings.
Skills Gap and Workforce Training
Security: Challenges also arise from the skills gap in the workforce regarding the adoption and utilization of AI and IoT technologies. As Industry 0 evolves, there is a growing need for professionals who are well-versed in these advanced technologies and can effectively leverage them to drive innovation and growth.
A: Addressing the skills gap requires investing in training programs and educational opportunities to upskill current employees and attract new talent with the necessary expertise in AI and IoT. Organizations must prioritize developing a workforce that can navigate the complexities of Industry 0 and maximize the benefits it offers.
To wrap up
To conclude, the integration of Artificial Intelligence (AI) and Internet of Things (IoT) in the industry, known as Industry 4.0, is revolutionizing the way businesses operate.
By combining the analytical power of AI with the connectivity of IoT devices, companies can streamline processes, optimize efficiency, and make data-driven decisions in real-time. This fusion of technologies is reshaping industries across the globe, leading to increased productivity and competitiveness.
For more in-depth information on how AI and IoT are integrated in Industry 4.0, you can read the article “Industrial AIoT: How AI and IoT are Integrated in Industry 4.0” here.
As we move further into the age of digital transformation, the seamless collaboration between AI and IoT will continue to drive innovation and redefine the industrial landscape.
FAQ
Q: What is Industry 0?
A: Industry 0 is a term used to describe the upcoming era of industrial transformation where artificial intelligence (AI) and the Internet of Things (IoT) play a crucial role in revolutionizing the way industries operate.
Q: How does AI contribute to Industry 0?
A: AI enhances Industry 0 by enabling machines to analyze data, make decisions, and perform tasks autonomously, leading to increased efficiency, productivity, and cost savings in industrial settings.
Q: What is the significance of IoT in Industry 0?
A: IoT devices in Industry 0 connect machines, sensors, and other equipment to the internet, allowing real-time data collection, analysis, and monitoring, which enables predictive maintenance, improved safety, and optimized processes in industries.
Stay tuned for more insights and tips on navigating visit our homepage for more articles.