It’s necessary to grasp the foundational elements of Industry 0 to navigate the future of manufacturing. Industry 0 represents the revolution in industrial processes through the integration of cutting-edge technologies like AI, IoT, and automation. Understanding the core components such as data analytics, smart machines, and interconnected systems is crucial for businesses aiming to thrive in this new era of industry. Let’s probe into the fundamental aspects that define Industry 0 and its implications for the global market.
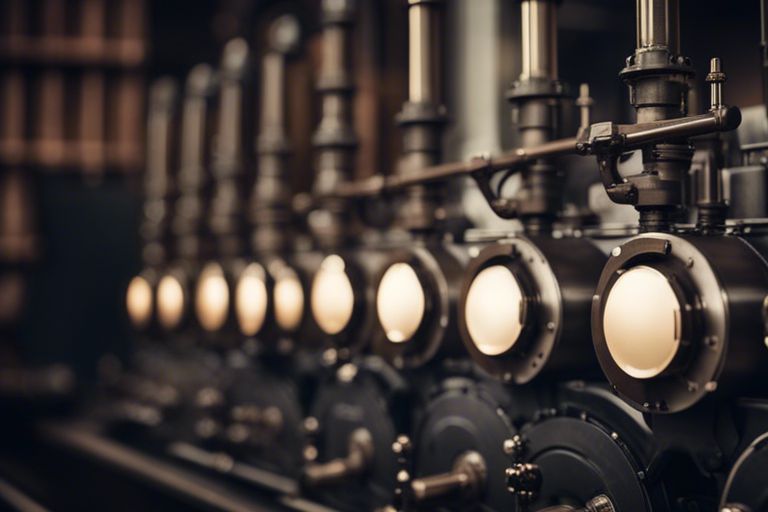
Key Takeaways:
- Industry 0 is the foundation: Industry 0 marks the beginning of the Industrial Revolution, characterized by the use of water and steam power in production processes.
- Mechanization is a key component: The shift towards mechanized processes in Industry 0 led to increased efficiency and productivity in manufacturing.
- Introduction of assembly lines: Henry Ford’s development of the assembly line during Industry 0 revolutionized mass production and standardized manufacturing processes.
- Impact on the workforce: Industry 0 brought significant changes to the workforce, with new skills required to operate machinery and manage production lines effectively.
- Paving the way for future industries: The innovations and advancements during Industry 0 laid the groundwork for further industrial revolutions, shaping the industries we see today.
Defining Industry 0
Your journey to understanding Industry 0 begins with a look back at its roots in the historical context of industrial revolutions. This foundation will pave the way for grasping the evolution of Industry 0 and its significance in shaping the future of industries worldwide.
Historical Context
Industry 0 traces its origins back to the Industrial Revolution, a period marked by significant advancements in manufacturing, transportation, and communication. This era laid the groundwork for subsequent industrial revolutions, each building upon the innovations of its predecessor.
Evolution of Industrial Revolutions
Historical progression has seen the evolution from Industry 1.0 characterized by mechanization and steam power, through Industry 2.0 fueled by electricity and mass production, then Industry 3.0 marked by automation and computerization. Now, we stand on the cusp of Industry 4.0, also known as the Fourth Industrial Revolution, driven by technologies like artificial intelligence, the Internet of Things, and automation. Industry 0 represents the next frontier, pushing the boundaries even further with advanced technologies that revolutionize the way we work and interact with machines.
Understanding the evolution of industrial revolutions is crucial in grasping the transformative power of Industry 0. This paradigm shift holds the potential to redefine industries and create new opportunities for growth and innovation. However, it also poses challenges in terms of workforce readiness and cybersecurity vulnerabilities. By delving into the core components of Industry 0, we can gain a deeper understanding of its implications for the future of work and industry as a whole.
Core Principles
If we investigate the core principles of Industry 0, we come across three fundamental components that drive the advancements in this era: interoperability, information transparency, and technical assistance. These principles serve as the backbone of Industry 0, setting the stage for a seamlessly connected and efficient manufacturing environment.
Interoperability
Interoperability is the ability of different systems, devices, and applications to seamlessly work together without any hindrance. In Industry 0, this principle ensures that various machines and technologies can communicate with each other, share data, and coordinate actions in real time. This seamless integration of systems leads to enhanced productivity, reduced downtime, and improved decision-making processes.
Information Transparency
For Information Transparency to be fully realized in Industry 0, data collection and sharing play a crucial role. Real-time access to accurate and relevant information empowers manufacturers to make informed decisions swiftly. This transparency across all levels of operations facilitates better collaboration, improved predictive maintenance, and optimized resource allocation.
A key aspect of Information Transparency is the accessibility and reliability of data. Manufacturers rely on a robust infrastructure to gather, store, and analyze data effectively. By ensuring data integrity and security, companies can trust the information they base their decisions on, leading to more streamlined and efficient operations.
Technical Assistance
Core to Industry 0 is the concept of Technical Assistance, which involves leveraging advanced technologies such as artificial intelligence, machine learning, and robotics to enhance manufacturing processes. These technologies provide invaluable support to workers, enabling them to perform tasks more efficiently and accurately. With the help of Technical Assistance, manufacturers can achieve higher levels of precision, automation, and scalability in their operations.
With Technical Assistance, companies can overcome traditional limitations and explore new possibilities in the manufacturing landscape. By harnessing the power of cutting-edge technologies, organizations can drive innovation, improve productivity, and stay ahead of the competition in the rapidly evolving Industry 0 environment.
Key Technologies
Once again, Industry 0 relies on several key technologies that form the backbone of its operations. These technologies work synergistically to bring about a new era of industrial revolution. Let’s investigate the three key components that define Industry 0: Artificial Intelligence, Internet of Things (IoT), and Cyber-Physical Systems.
Artificial Intelligence
On the forefront of Industry 0 is Artificial Intelligence (AI), which plays a crucial role in automating processes, predicting outcomes, and optimizing workflows. AI algorithms can analyze vast amounts of data at incredible speeds, identifying patterns and insights that human operators might miss. This results in increased efficiency, reduced downtime, and improved decision-making capabilities.
Internet of Things (IoT)
An integral part of Industry 0, the Internet of Things (IoT) refers to the network of interconnected devices that collect and exchange data. IoT devices in smart factories can monitor equipment performance in real time, trigger maintenance alerts, and enable remote operation and control. This leads to improved productivity, resource efficiency, and safety in industrial settings.
Industries can leverage IoT technology to create connected ecosystems where machines communicate seamlessly with each other, optimizing production processes and reducing costs.
Cyber-Physical Systems
Systems in Industry 0 integrate computing, networking, and physical processes to create Cyber-Physical Systems. These systems enable real-time monitoring, control, and automation of physical processes, blurring the line between the digital and physical worlds.
Cyber-physical systems enhance operational efficiency, enable predictive maintenance, and facilitate autonomous decision-making, transforming industries across sectors.
Internet

Data-Driven Decision Making
Not only is data an important component of Industry 4.0, but utilizing this data to make informed decisions is crucial for success in today’s rapidly evolving industrial landscape. Data-driven decision making involves collecting, analyzing, and interpreting data from various sources to gain valuable insights that can drive strategic actions.
Real-Time Analytics
With real-time analytics, companies can access and analyze data as it is generated, allowing for immediate insights and quick decision-making. This capability is particularly crucial in fast-paced industries where timely decisions can make a significant impact on operations and overall efficiency.
Predictive Maintenance
With predictive maintenance, companies can leverage data and analytics to predict when equipment is likely to fail, allowing for proactive maintenance to be performed before issues arise. This approach can prevent costly downtime, increase equipment lifespan, and improve overall productivity.
This proactive maintenance strategy involves analyzing historical data, sensor readings, and other relevant information to identify patterns and trends that indicate potential equipment failures. By addressing issues before they occur, companies can save on maintenance costs and prevent unexpected downtimes that can disrupt operations.
Supply Chain Optimization
Chain optimization involves using data analytics to streamline and enhance supply chain processes, from sourcing materials to delivering finished products. Analytics can help companies optimize inventory levels, reduce lead times, and improve overall efficiency in the supply chain.
By leveraging data to gain insights into supplier performance, demand forecasting, and production scheduling, companies can make smarter decisions that lead to cost savings, improved customer satisfaction, and a more agile supply chain. This optimization is important in today’s competitive business environment where responsiveness and efficiency are paramount.
Human-Centric Approach
For a successful transition to Industry 4.0, a human-centric approach is necessary. This approach focuses on leveraging technology to empower and enhance the capabilities of the workforce.
Augmented Workforce
HumanCentric augmentation of the workforce involves integrating advanced technologies like artificial intelligence and machine learning to assist employees in their tasks. This approach aims to improve efficiency, accuracy, and safety in the workplace while allowing humans to focus on more strategic and creative endeavors.
Skills Training and Development
Skills training and development are crucial in preparing the workforce for the demands of Industry 4.0. Continuous learning and upskilling programs ensure that employees have the necessary skills to work effectively alongside automated systems.
To ensure a smooth transition, companies must invest in comprehensive training programs that address both technical skills and soft skills such as adaptability, critical thinking, and problem-solving.
Workforce Redefinition
Workforce redefinition involves reshaping roles and responsibilities to accommodate the integration of technology. This may include restructuring job roles, creating new positions focused on managing automated systems, and fostering a culture of innovation and collaboration.
The key to a successful workforce redefinition is ensuring that employees feel valued, engaged, and empowered in their new roles, fostering a positive work environment where innovation thrives.
Approach
Implementation Challenges
Unlike the straightforward adoption process of Industry 4.0, moving towards Industry 0 poses several implementation challenges. The shift to Industry 0 requires significant infrastructure upgrades, such as the integration of legacy systems with cutting-edge technology and the implementation of robust connectivity solutions.
Infrastructure Upgrades
For Industry 0 to function effectively, old machinery may need to be retrofitted with sensors and smart technologies to enable data collection and analysis. This process can be costly and time-consuming, requiring careful planning and expertise to ensure seamless integration within existing infrastructures.
Cybersecurity Concerns
On the cybersecurity front, transitioning to Industry 0 opens up a host of new vulnerabilities that must be addressed. The interconnected nature of Industry 0 systems increases the potential entry points for cyber attacks, making data security a top priority for organizations.
Cybersecurity measures must be implemented at every level of the Industry 0 framework, from individual devices to centralized control systems. Regular updates, robust encryption protocols, and continuous monitoring are necessary to safeguard sensitive data and mitigate cybersecurity risks.
Change Management
Challenges in change management also arise during the implementation of Industry 0. Organizational structures, workflows, and employee roles may need to be redefined to align with the new operational paradigm introduced by Industry 0 technologies.
A culture shift towards embracing innovation and adaptability is crucial to successfully navigate the changes brought about by Industry 0. Training programs, clear communication strategies, and effective leadership are key components in managing organizational transitions and ensuring the smooth adoption of Industry 0 practices.
Summing up
Hence, understanding the key components of Industry 0 is crucial for businesses looking to stay competitive and innovative in today’s rapidly evolving landscape. By grasping concepts such as automation, IoT, data analytics, and cybersecurity, organizations can harness the power of Industry 0 to enhance efficiency, productivity, and customer experiences. For a deeper probe the next phase of the industrial revolution, explore What is Industry 4.0? for insights and trends shaping the future of manufacturing and beyond.
FAQ
Q: What is Industry 0?
A: Industry 0 refers to the earliest stage of industrial development, characterized by manual labor and minimal use of machinery or automation.
Q: What are the key components of Industry 0?
A: The key components of Industry 0 include human labor, basic tools, simple machines, and limited technological advancements.
Q: How does Industry 0 compare to modern industrial practices?
A: Industry 0 is significantly less efficient and productive compared to modern industrial practices, which heavily rely on automation, AI, and advanced technologies to streamline operations and increase output.
Stay tuned for more insights and tips on navigating visit our homepage for more articles.